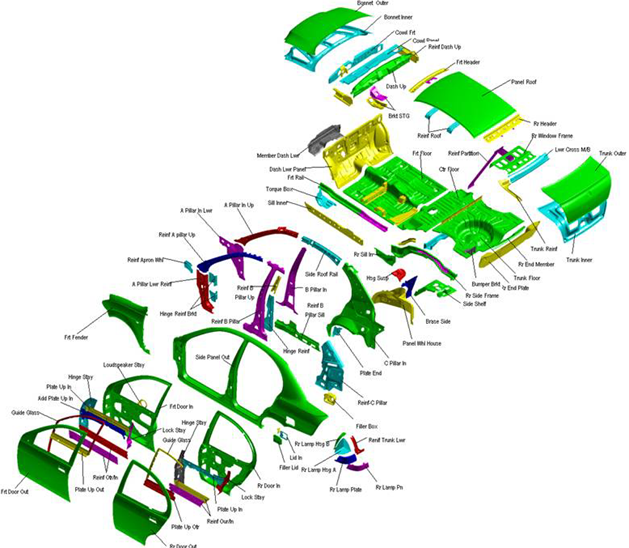
In today’s world, the competition among global auto manufacturers is becoming more and more fierce, the average lifespan of models is constantly shortening, and the speed of launching new products of vehicle companies is accelerating. higher requirements. The traditional auto body serial development model has been unable to meet the requirements of industry development due to its own shortcomings, and synchronous engineering came into being. The so-called Simultaneous Engineering (SE) is a working mode for parallel and integrated design of product development and related processes. The development speed is directly determined by the development speed of the mold. Stamping SE plays an important role in shortening the mold development cycle, improving material utilization, reducing costs and improving stamping manufacturability.
Stamping SE improves stamping manufacturability
The traditional automobile body development work adopts the serial engineering method, which is easy to cause the front and back to be disconnected. Due to the inability to consider process planning, quality assurance and manufacturing process issues as early as possible in the process, some problems cannot be exposed and solved until later, resulting in large design changes, long product development cycles and high product costs. We all know that the later errors are discovered in the product life cycle, the more costly they are. The stamping SE project timely feeds back issues such as process planning and manufacturing manufacturability to the product department, which can eliminate “errors” in the design stage.
- Realize a reasonable definition of product materials
If the original product-defined material cannot be used to punch out qualified parts after the mold is processed, the debugging cycle of the mold will be increased, and even the mold will be scrapped. If the material is replaced at this time, the body collision will not pass. Therefore, in the stamping SE process, it is necessary to verify the rationality of the product material definition with the help of CAE analysis software (Autoform, Pam-stamp).
Figures 1 and 2 show the analysis results of different materials used for the channel reinforcement plate and seat beam in a certain vehicle model. As shown in Figure 2, it can be seen from 2c that there is a risk of cracking in the local area formed with the B340LA material initially defined by the product. When the material is changed to B170P1, the analysis result is 2b, and the risk of forming cracking is eliminated. After this information was fed back to the product department during the stamping SE process, the product department changed the material to B170P1. In order to ensure the strength of the body under this material, the design department adjusted the body structure locally, which not only reduces the debugging cycle of the mold and the risk of mold scrap, but also solves the problem that the body cannot pass through the collision of the later replacement material.